Home> Company News> Pressure Adjusting Valves 101: An Introduction to Their Function and Importance

- AddressToh Guan Centre, 31/F,69 Toh Guan Rd E, Singapore 608609
- Factory AddressToh Guan Centre, 31/F,69 Toh Guan Rd E, Singapore 608609
- Worktime9:00-18:00
- Phone(Working Time)0065-31591578
- Phone(Nonworking Time)0065-31591578
- Fax0065-31591339
Pressure Adjusting Valves 101: An Introduction to Their Function and Importance
2023-04-25 14:07:28Pressure adjusting valves are essential components of hydraulic systems that regulate the fluid flow and pressure to ensure optimal system performance. These valves work by controlling the pressure of the fluid flowing through the system, protecting it from damage due to excessive pressure. Pressure adjusting valves can be found in a wide range of industries, including automotive, construction, and manufacturing.
Proper selection and maintenance of pressure adjusting valves are critical for the safety, reliability, and efficiency of hydraulic systems. This article provides an overview of pressure adjusting valves, their types, functions, and factors to consider when selecting them. It also covers common issues with pressure adjusting valves and troubleshooting techniques. Finally, the article concludes with the importance of pressure adjusting valves and their role in the future of hydraulic systems.

Types of Pressure Adjusting Valves
Pressure adjusting valves are essential components in hydraulic systems, as they regulate the pressure of hydraulic fluid to maintain optimal system performance and prevent damage to equipment. There are several types of pressure adjusting valves available, each with its own unique features and applications. Here are some of the most common types of pressure adjusting valves:
-
Direct-Acting Relief Valves Direct-acting relief valves are used in hydraulic systems to regulate pressure by controlling the flow of hydraulic fluid to the system. These valves operate by opening when the pressure exceeds a set limit, allowing fluid to flow back to the reservoir and reducing the pressure in the system.
-
Pilot-Operated Relief Valves Pilot-operated relief valves are similar to direct-acting relief valves, but they use a pilot valve to control the flow of hydraulic fluid to the system. This makes them more precise and accurate than direct-acting relief valves, as they can be adjusted to respond to specific pressure ranges.
-
Sequence Valves Sequence valves are used to ensure that one hydraulic cylinder or actuator operates before another. They work by controlling the pressure required to operate each cylinder or actuator, allowing for more precise and controlled movement of equipment.
-
Counterbalance Valves Counterbalance valves are used to maintain the pressure in a hydraulic system and prevent loads from dropping or falling. They work by providing a back pressure to prevent the load from moving, allowing for safer and more efficient operation of hydraulic equipment.
-
Pressure Reducing Valves Pressure reducing valves are used to reduce the pressure of hydraulic fluid in a system. They work by diverting a portion of the fluid back to the reservoir, reducing the pressure and preventing damage to equipment.
Understanding the different types of pressure adjusting valves available can help in selecting the best valve for a specific hydraulic application.
Function of Pressure Adjusting Valves
Pressure adjusting valves play a critical role in controlling the flow and pressure of fluids within hydraulic systems. They function by adjusting the pressure of fluid within a hydraulic system to a set level and maintaining it at that level, regardless of fluctuations in flow or system demand.
There are several common types of pressure adjusting valves, each with its own unique function:
-
Direct-acting relief valves: These valves are designed to limit the maximum pressure within a hydraulic system by diverting excess fluid flow back to the system reservoir. They operate by using a spring-loaded valve that opens when system pressure exceeds a preset limit, allowing fluid to flow back to the reservoir until the pressure drops back down to the desired level.
-
Pilot-operated relief valves: Similar to direct-acting relief valves, pilot-operated relief valves also divert excess fluid flow back to the reservoir. However, they use a pilot valve to control the opening and closing of the main relief valve, allowing for more precise pressure control and faster response times.
-
Sequence valves: These valves are used to control the sequence in which hydraulic actuators or motors are activated in a system. They allow for one actuator to complete its task before another is activated, preventing overload and ensuring optimal system performance.
-
Counterbalance valves: These valves are designed to control the movement of heavy loads, such as those found in construction or agricultural equipment. They work by providing a backpressure to the actuator, preventing it from moving under the weight of the load.
-
Pressure reducing valves: As the name suggests, pressure reducing valves are used to reduce the pressure of fluid within a hydraulic system. They work by diverting fluid to a low-pressure zone, effectively reducing the overall pressure of the system.
Overall, pressure adjusting valves are critical components in hydraulic systems and are used in a wide range of applications, including aerospace, automotive, construction, and manufacturing industries. By regulating the pressure of fluid within hydraulic systems, pressure adjusting valves ensure that systems operate at optimal levels, reducing wear and tear on components and improving system performance.
Factors to Consider When Selecting Pressure Adjusting Valves
Selecting the right pressure adjusting valve is critical for optimal performance and safety in hydraulic systems. When choosing a pressure adjusting valve, several factors should be considered to ensure proper operation and compatibility with the system.
Operating Pressure Range
The operating pressure range of the valve should match the system's pressure requirements. If the valve is unable to regulate pressure within the system's operating range, the system may fail or become damaged. It is essential to select a valve with an appropriate pressure range to ensure optimal performance and safety.
Flow Rate
Flow rate refers to the volume of fluid that passes through the valve over time. The valve must be able to handle the flow rate required by the system. If the valve is unable to control the flow rate, it may lead to system damage or inefficiencies. It is crucial to choose a valve that can accommodate the required flow rate to prevent these issues.
Valve Size and Port Configuration
The valve's size and port configuration must be compatible with the system's requirements. If the valve is too small, it may restrict flow and cause pressure drops, leading to system inefficiencies. If the valve is too large, it may not regulate pressure accurately, leading to potential system damage. Choosing the right valve size and port configuration is essential for optimal performance.
Response Time
The response time of the valve is critical for ensuring that the system operates efficiently and safely. A slow response time may lead to pressure spikes or drops, causing damage to the system. A quick response time is necessary to maintain pressure within the system's operating range. It is important to choose a valve with a response time that matches the system's requirements.
Material Compatibility
The valve's material must be compatible with the fluid and system components. Incompatible materials can corrode or degrade, leading to system damage and inefficiencies. It is essential to choose a valve made from materials that are compatible with the system's fluid and components to prevent these issues.
Installation and Maintenance Requirements
Proper installation and maintenance are critical for the optimal performance and longevity of the valve. The valve should be installed according to the manufacturer's instructions to ensure proper function. Regular maintenance, including inspection and cleaning, is necessary to prevent issues and ensure optimal performance.
By considering these factors when selecting a pressure adjusting valve, the hydraulic system can operate safely and efficiently. Proper selection and maintenance of the valve are critical for ensuring optimal performance and preventing system damage or failures.
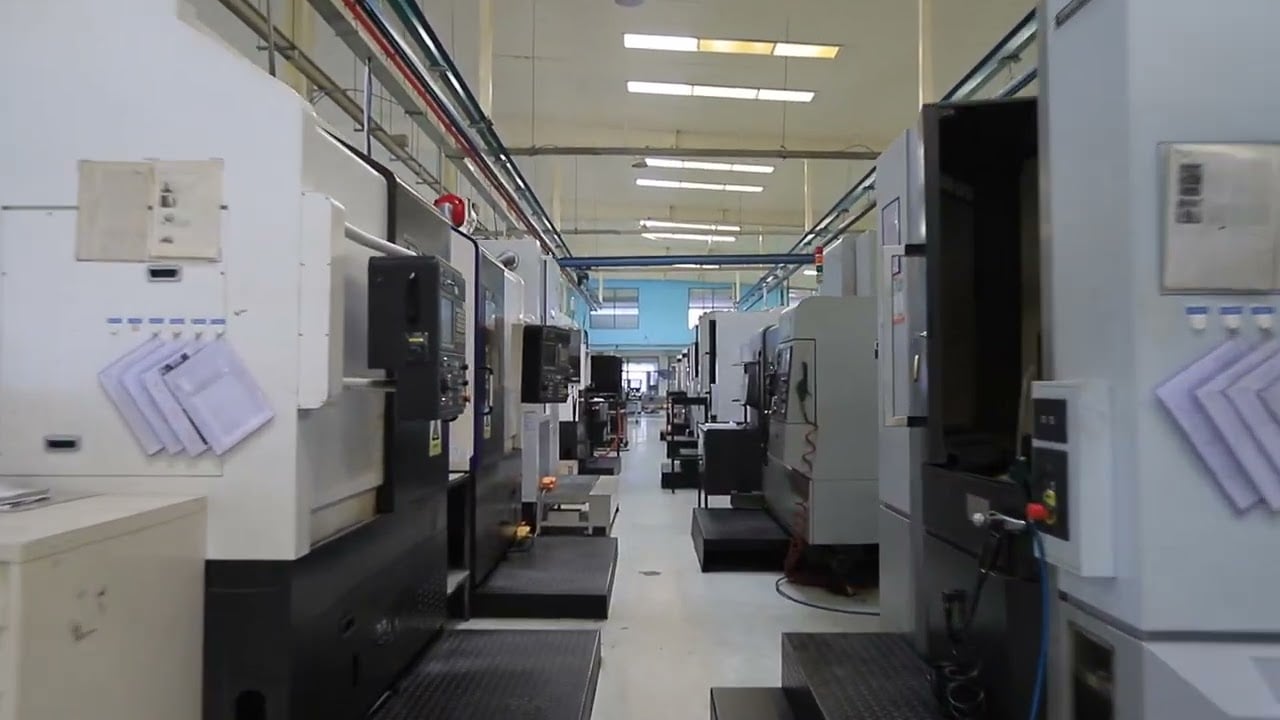
Troubleshooting Common Issues with Pressure Adjusting Valves
Pressure adjusting valves play a crucial role in hydraulic systems by regulating fluid flow and controlling pressure. However, like any mechanical component, pressure adjusting valves can experience malfunctions and issues that affect their performance. In this section, we will discuss common issues with pressure adjusting valves and how to troubleshoot them.
Symptoms of Malfunctioning Pressure Adjusting Valves
One of the most common symptoms of a malfunctioning pressure adjusting valve is a loss of pressure regulation. If the valve fails to regulate pressure properly, the system may experience pressure spikes or drops, which can lead to damage or failure of system components. Another common symptom is leakage, which can result from worn or damaged seals or valves. A noisy valve may also indicate a problem, as it could be caused by cavitation or other issues.
Diagnosing and Fixing Common Issues
When troubleshooting a pressure adjusting valve, it is important to first identify the specific problem. This can often be done by monitoring the system pressure and flow rate and observing the behavior of the valve. Once the problem has been identified, the following steps can be taken to fix it:
-
Inspect the valve and surrounding components for signs of wear, damage, or contamination.
-
Check the valve for proper installation and adjustment, ensuring that it is set to the correct pressure range and that the flow rate is within the valve's capacity.
-
Replace worn or damaged seals, valves, or other components as needed.
-
Check the hydraulic fluid for contamination or other issues, and replace it if necessary.
-
Adjust or recalibrate the valve as needed to ensure proper function.
-
Monitor the system for further issues and perform regular maintenance to prevent future problems.
It is important to note that some issues with pressure adjusting valves may require the expertise of a professional technician, particularly if the problem is complex or requires specialized equipment. In such cases, it is advisable to consult with a qualified hydraulic specialist.
Conclusion
In summary, pressure adjusting valves play a crucial role in hydraulic systems by regulating pressure and flow rate. By selecting the right type of valve and ensuring proper maintenance, hydraulic systems can operate at optimal levels of efficiency and reliability.
As technology continues to evolve, pressure adjusting valve technology is also expected to improve, with advances in design and materials leading to greater precision and durability. Additionally, there may be increased integration of pressure adjusting valves with other components of hydraulic systems, allowing for even more efficient and reliable operation.
In conclusion, pressure adjusting valves are an essential component of hydraulic systems, and their proper selection, installation, and maintenance is critical to ensuring optimal performance and safety. As the technology continues to advance, we can expect to see even greater benefits from these valuable components.
Mud pump bearings Turntable bearings Agricultural bearings Angular Contact Bearings Duplex Angular Contact Bearings Industrial bearings Iron and steel industry bearings Power transmission bearing Hydrostatic centripetal bearing Ball Thrust Bearings Papermaking Machinery bearings Agricultural machinery bearing McGILL bearing Rexroth pump assay Komatsu motor parts BOSCH Fuel injector Hitachi excavator parts Axial Piston Pumps Sauer Danfoss pump Eaton pump parts Nachi pump assay Linde pump Mining Construction Ball Bearings Linear Bearings vane pumps gear pumps inc piston pumps Thin-Section Ball Bearings Adapter Sleeves pressure valves gear reducer relief valves Mcgill Bearing Die & Mold Plain-Bearing Bushings FAG Bearing Singapore SKF bearing Accessories SKF bearing Housing SKF bearing shaft seals SKF Bearing units Bearing Distributors Inventory Oilfield mud pump bearings Heavy-Duty Shaker Screen Spherical Double row double row tapered roller bearings (inch series) Multi-Row Roller Bearings NTN Four Row Cylindrical Roller Bearings NTN SL Type Cylindrical Roller Bearings NTN SL Type Cylindrical Roller Bearings for Sheaves NTN Single Row Tapered Roller Bearings NTN Double Row Tapered Roller Bearings NTN Four Row Tapered Roller Bearings NTN Spherical Roller Bearings NTN Thrust Bearings NTN Bearings for special applications NTN DOUBLE-ROW CYLINDRICAL ROLLER BEARINGS NSK FULL-COMPLEMENT CYLINDRICAL ROLLER BEARINGS NSK SINGLE-ROW TAPERED ROLLER BEARINGS NSK YUKEN Piston pump DOUBLE-ROW TAPERED ROLLER BEARINGS NSK SPHERICAL ROLLER BEARINGS NSK SINGLE-DIRECTION THRUST BALL BEARINGS NSK CYLINDRICAL ROLLER THRUST BEARINGS NSK TAPERED ROLLER THRUST BEARINGS NSK SPHERICAL THRUST ROLLER BEARINGS NSK ROLLING BEARINGS FOR STEEL MILLS NSK SEALED-CLEAN FOUR-ROW TAPERED ROLLER BEARINGS NSK FOUR-ROW CYLINDRICAL ROLLER BEARINGS NSK DOUBLE-ROW TAPERED ROLLER BEARINGS NSK Roll Bearings for Mills NSK Ball Bearings NSK TAPERED ROLLER THRUST BEARINGS For Adjusting Screws NSK Thin Section Bearings Kaydon Double row double row tapered roller bearings (inch series) Double direction thrust tapered roller bearings Full complement Tapered roller Thrust bearing Thrust cylindrical roller bearings Thrust spherical roller bearings Sealed Four Row Tapered Roller Bearings Four row tapered roller bearings Double outer double row tapered roller bearings TDO double-row tapered roller bearings Single row tapered roller bearings inch Double inner double row tapered roller bearings TDI Double inner double row tapered roller bearings inch Spherical roller bearing Four row cylindrical roller bearings Single row cylindrical roller bearings Full row of cylindrical roller bearings Double row cylindrical roller bearings Double row full complement cylindrical roller bearings Four point contact ball bearings Double row angular contact ball bearings Deep groove ball bearings ANGULAR CONTACT THRUST BALL BEARINGS TYPE TVL DTVL angular contact thrust ball bearing. TP thrust cylindrical roller bearing TPS thrust cylindrical roller bearing THRUST SPHERICAL ROLLER BEARINGS TYPES TSR-EJ AND TSR-EM TTHD THRUST TAPERED ROLLER BEARINGS TTHDFL thrust tapered roller bearing TTHDFLSA THRUST TAPERED ROLLER BEARINGS THRUST TAPERED ROLLER BEARINGS TYPES TTSP, TTSPS AND TTSPL THRUST TAPERED ROLLER BEARINGS – TYPES TTC, TTCS AND TTCL SCREWDOWN BEARINGS – TYPES TTHDSX/SV AND TTHDFLSX/SV THRUST TAPERED ROLLER BEARING TYPES TTDWK AND TTDFLK CROSSED ROLLER BEARINGS TXR Tapered Roller bearings double-row • Type TDO Tapered Roller bearings double-row TDI TDIT Tapered Roller Bearings double-row TNA Tapered Roller Bearings double-row TNASWE Tapered Roller Bearings double-row Spacer assemblies TTVS TTSP TTC TTCS TTCL tapered roller thrust BEARINGS Heavy-Duty Shaker Screen Spherical Roller Bearings Timken SPHERICAL ROLLER BEARINGS CYLINDRICAL ROLLER BEARINGS ONE-ROW METRIC ISO SERIES CYLINDRICAL ROLLER BEARINGS one-row STANDARD SERIES CYLINDRICAL ROLLER BEARINGS FULL-COMPLEMENT NCF CYLINDRICAL ROLLER BEARINGS TWO-Row Four-Row Cylindrical Roller Bearings CYLINDRICAL ROLLER BEARINGS HJ SERIES CYLINDRICAL ROLLER BEARINGS 5200 A5200 metric series HeavY-duty needle roller bearings four-row cylindrical roller Bearing assembly four-row cylindrical roller Bearing inner ring Outer assembly four-row tapered roller Bearings • tQow – 2tdiw Timken Sealed roll neck Bearings four-row tapErEd rollEr BEaringS tQitS TnasWH TWo-roW TaPered roller bearings TdiT TnaT two-row tapErEd rollEr BEaringS tdik THrusT TaPered roller bearings TTdFlk, TTdW and TTdk bearings screwdown systems thrust tapered rollEr Bearings Thrust spherical roller bearing Mud pump bearings TOKYO-KEIKI piston pump TOKYO-KEIKI vane pump DAIKIN piston pump DAIKIN vane pump DAIKIN Rotor pump VICKERS Piston pump Vickers vane pump VICKERS gear pump NACHI gear pump NACHI piston pump Rexroth A1VO Rexroth A10VSO Rexroth AA4VSO Rexroth A15VSO Rexroth AZPF parker PV piston pump parker PVP piston pump parker PAVC piston pump parker vane pump Multi-Row Roller Bearings NTN Four Row Cylindrical Roller Bearings NTN SL Type Cylindrical Roller Bearings NTN SL Type Cylindrical Roller Bearings for Sheaves NTN Single Row Tapered Roller Bearings NTN Double Row Tapered Roller Bearings NTN Four Row Tapered Roller Bearings NTN Spherical Roller Bearings NTN Thrust Bearings NTN Bearings for special applications NTN DOUBLE-ROW CYLINDRICAL ROLLER BEARINGS NSK FULL-COMPLEMENT CYLINDRICAL ROLLER BEARINGS NSK SINGLE-ROW TAPERED ROLLER BEARINGS NSK YUKEN Piston pump DOUBLE-ROW TAPERED ROLLER BEARINGS NSK SPHERICAL ROLLER BEARINGS NSK SINGLE-DIRECTION THRUST BALL BEARINGS NSK CYLINDRICAL ROLLER THRUST BEARINGS NSK TAPERED ROLLER THRUST BEARINGS NSK SPHERICAL THRUST ROLLER BEARINGS NSK ROLLING BEARINGS FOR STEEL MILLS NSK SEALED-CLEAN FOUR-ROW TAPERED ROLLER BEARINGS NSK FOUR-ROW CYLINDRICAL ROLLER BEARINGS NSK DOUBLE-ROW TAPERED ROLLER BEARINGS NSK Roll Bearings for Mills NSK CROSSED-ROLLER BEARINGS NSK Ball Bearings NSK TAPERED ROLLER THRUST BEARINGS For Adjusting Screws NSK Roller Bearings NSK Thin Section Bearings Kaydon Double row double row tapered roller bearings (inch series) Double direction thrust tapered roller bearings Full complement Tapered roller Thrust bearing Thrust cylindrical roller bearings Thrust spherical roller bearings Sealed Four Row Tapered Roller Bearings Four row tapered roller bearings Double outer double row tapered roller bearings TDO double-row tapered roller bearings Single row tapered roller bearings inch Double inner double row tapered roller bearings TDI Single row tapered roller bearings Double inner double row tapered roller bearings inch Split spherical roller bearings Spherical roller bearing Four row cylindrical roller bearings Single row cylindrical roller bearings Full row of cylindrical roller bearings Double row cylindrical roller bearings Double row full complement cylindrical roller bearings Four point contact ball bearings Double row angular contact ball bearings Deep groove ball bearings ANGULAR CONTACT THRUST BALL BEARINGS TYPE TVL DTVL angular contact thrust ball bearing. TP thrust cylindrical roller bearing TPS thrust cylindrical roller bearing THRUST SPHERICAL ROLLER BEARINGS TYPES TSR-EJ AND TSR-EM TTHD THRUST TAPERED ROLLER BEARINGS TTHDFL thrust tapered roller bearing TTHDFLSA THRUST TAPERED ROLLER BEARINGS THRUST TAPERED ROLLER BEARINGS TYPES TTSP, TTSPS AND TTSPL THRUST TAPERED ROLLER BEARINGS – TYPES TTC, TTCS AND TTCL SCREWDOWN BEARINGS – TYPES TTHDSX/SV AND TTHDFLSX/SV THRUST TAPERED ROLLER BEARING TYPES TTDWK AND TTDFLK CROSSED ROLLER BEARINGS TXR Tapered Roller bearings double-row • Type TDO Tapered Roller bearings double-row TDI TDIT Tapered Roller Bearings double-row Spacer assemblies TTVS TTSP TTC TTCS TTCL tapered roller thrust BEARINGS Heavy-Duty Shaker Screen Spherical Roller Bearings Timken SPHERICAL ROLLER BEARINGS CYLINDRICAL ROLLER BEARINGS ONE-ROW METRIC ISO SERIES CYLINDRICAL ROLLER BEARINGS one-row STANDARD SERIES CYLINDRICAL ROLLER BEARINGS FULL-COMPLEMENT NCF CYLINDRICAL ROLLER BEARINGS TWO-Row Four-Row Cylindrical Roller Bearings CYLINDRICAL ROLLER BEARINGS HJ SERIES CYLINDRICAL ROLLER BEARINGS 5200 A5200 metric series HeavY-duty needle roller bearings four-row cylindrical roller Bearing assembly four-row cylindrical roller Bearing inner ring Outer assembly Timken Sealed roll neck Bearings four-row tapErEd rollEr BEaringS tQitS TnasWH TWo-roW TaPered roller bearings TdiT TnaT two-row tapErEd rollEr BEaringS tdik THrusT TaPered roller bearings TTdFlk, TTdW and TTdk bearings screwdown systems thrust tapered rollEr Bearings Thrust spherical roller bearing Mud pump bearings TOKYO-KEIKI piston pump TOKYO-KEIKI vane pump YUKEN vane pump DAIKIN piston pump DAIKIN vane pump DAIKIN Rotor pump VICKERS Piston pump Vickers vane pump VICKERS gear pump NACHI gear pump NACHI piston pump Rexroth A1VO Rexroth A10VSO Rexroth AA4VSO Rexroth A15VSO Rexroth AZPF parker PV piston pump parker PVP piston pump parker PAVC piston pump Main pump